Cost-Effective Techniques for Packaging Machine Repair and Upgrades
Cost-Effective Techniques for Packaging Machine Repair and Upgrades
Blog Article
Reliable Ways to Troubleshoot Common Issues in Packaging Equipment Procedure
In the realm of manufacturing and manufacturing, guaranteeing the seamless operation of product packaging equipments is vital to preserving performance and meeting due dates. Let's explore some effective approaches that can help in quickly resolving typical issues in product packaging machine operation.

Identifying Common Packaging Maker Problems
When repairing product packaging equipment troubles, it is essential to precisely determine usual concerns that might emerge during the packaging procedure. One typical issue run into in product packaging machines is improper securing. This can result in items not being safely packaged, running the risk of damages or contamination during transportation. One more regular issue is misalignment, where the packaging products or items are not correctly aligned, causing jams or misfeeds. In addition, mechanical damage on parts like belts, equipments, or chains can lead to irregular packaging or machine malfunctions.
Furthermore, concerns with sensing units can interrupt the product packaging process by failing to spot items or setting off improperly. packaging machine repair. Electrical troubles, such as defective circuitry or power supply problems, are also usual offenders behind product packaging equipment failures. Recognizing and promptly dealing with these typical issues are essential for preserving the efficiency and integrity of product packaging operations. By identifying these concerns at an early stage, drivers can prevent downtime, lower product waste, and make sure the smooth performance of product packaging equipment.
Doing Routine Maintenance Checks
Regularly carrying out extensive upkeep checks is essential for making sure the ideal efficiency and durability of packaging devices. By adhering to a structured upkeep timetable, possible issues can be recognized and fixed proactively, lessening downtime and expensive repair work. When carrying out routine maintenance checks, it is crucial to evaluate vital elements such as belts, chains, seals, and sensors for any indicators of wear or damages. Lubricating and cleansing moving parts can help protect against friction-related troubles and make certain smooth operation. Furthermore, inspecting and calibrating settings connected to rate, temperature level, and pressure can aid keep the equipment's efficiency and accuracy.
Additionally, performing normal assessments of electric links and controls can help stop electric breakdowns and make sure the safety and security of the device drivers. Documenting maintenance tasks and maintaining in-depth records of parts substitutes and repairs can help in tracking the device's efficiency over time and recognizing any type of recurring problems. Inevitably, a proactive method to routine maintenance checks is critical in taking full advantage of the efficiency and dependability of packaging devices.
Fixing Mechanical and electric Issues
Efficient troubleshooting of electric and mechanical troubles in product packaging devices calls for a methodical strategy and a deep understanding of the device's elements and operation. When dealing with electrical concerns, beginning by inspecting power sources, links, and control panels for any type of noticeable damages or loosened links.
On the mechanical front, problems like jams, misalignments, or extreme resonances can interfere with packaging operations. To deal with mechanical issues, carry out a comprehensive visual examination of relocating components, belts, chains, and equipments for signs of wear or damage. Lubrication of key components can protect against friction-related issues and guarantee smooth equipment procedure. Validating the alignment of elements and readjusting stress article where essential can fix concerns associated to misalignments or uneven activities in the product packaging equipment. By incorporating a methodical technique with a thorough understanding of the device's workings, efficient troubleshooting of electrical and mechanical troubles can be accomplished, lessening downtime and optimizing manufacturing output.
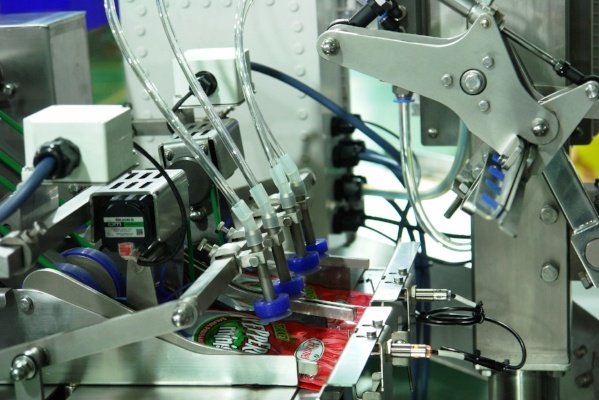
Optimizing Device Setups for Efficiency
To enhance the total efficiency of packaging machines, a critical facet includes fine-tuning and optimizing machine setups for maximum performance and result uniformity. Correctly adjusted maker settings can significantly influence the speed, precision, and high quality of the packaging procedure. Frequently monitoring and readjusting these device setups based on the specific needs of the packaging products and product can lead to increased effectiveness, reduced downtime, and improved total outcome top quality.
Carrying Out Preventive Upkeep Measures
Carrying out preventive upkeep steps is crucial for making sure the longevity and optimal efficiency of product packaging devices in commercial setups. Regular upkeep assists prevent unforeseen failures, reduces downtime, and eventually conserves time and cash for businesses. To efficiently carry out preventative upkeep, create a comprehensive maintenance routine describing jobs such as cleansing, lubricating, evaluating, and changing used components. This timetable should be followed vigilantly by qualified maintenance workers to make sure that the makers run at peak performance.
In enhancement to set up maintenance, it is vital to maintain complete documents of all maintenance activities Continue executed on the product packaging devices. These records can provide beneficial insights into the equipments' performance trends, aid identify persisting problems, and guide future upkeep efforts - packaging machine repair. Furthermore, investing in training programs for maker operators and maintenance team on appropriate maintenance treatments and techniques can significantly boost the efficiency of preventative maintenance actions. By focusing on preventive upkeep, companies can lengthen the lifespan of their product packaging machines, reduce disturbances in production, and preserve constant item quality.
Conclusion
To conclude, efficient troubleshooting of common issues in packaging machine operation involves look these up determining issues, doing routine maintenance checks, fixing electrical and mechanical concerns, enhancing device settings for performance, and applying preventative upkeep procedures. By adhering to these actions, drivers can make certain reputable and smooth operation of packaging devices, decreasing downtime and optimizing efficiency.
When troubleshooting packaging machine problems, it is critical to properly determine typical issues that might emerge during the packaging process.Effective troubleshooting of electrical and mechanical problems in packaging makers needs an organized technique and a deep understanding of the maker's elements and procedure.To boost the total efficiency of product packaging equipments, a crucial facet includes fine-tuning and enhancing maker setups for maximum effectiveness and result uniformity.Carrying out preventative maintenance steps is crucial for guaranteeing the durability and ideal performance of product packaging devices in industrial settings.In addition to set up upkeep, it is vital to keep detailed records of all maintenance activities carried out on the packaging devices.
Report this page